【取材】プラスオートメーションのショールーム ”cube" で見てきた、物流ロボットの実力
「物流ロボット」や「物流DX」などという単語を見ると、ものすごく特殊なことをする難しいことではないかと、身構える方が多いと思います。
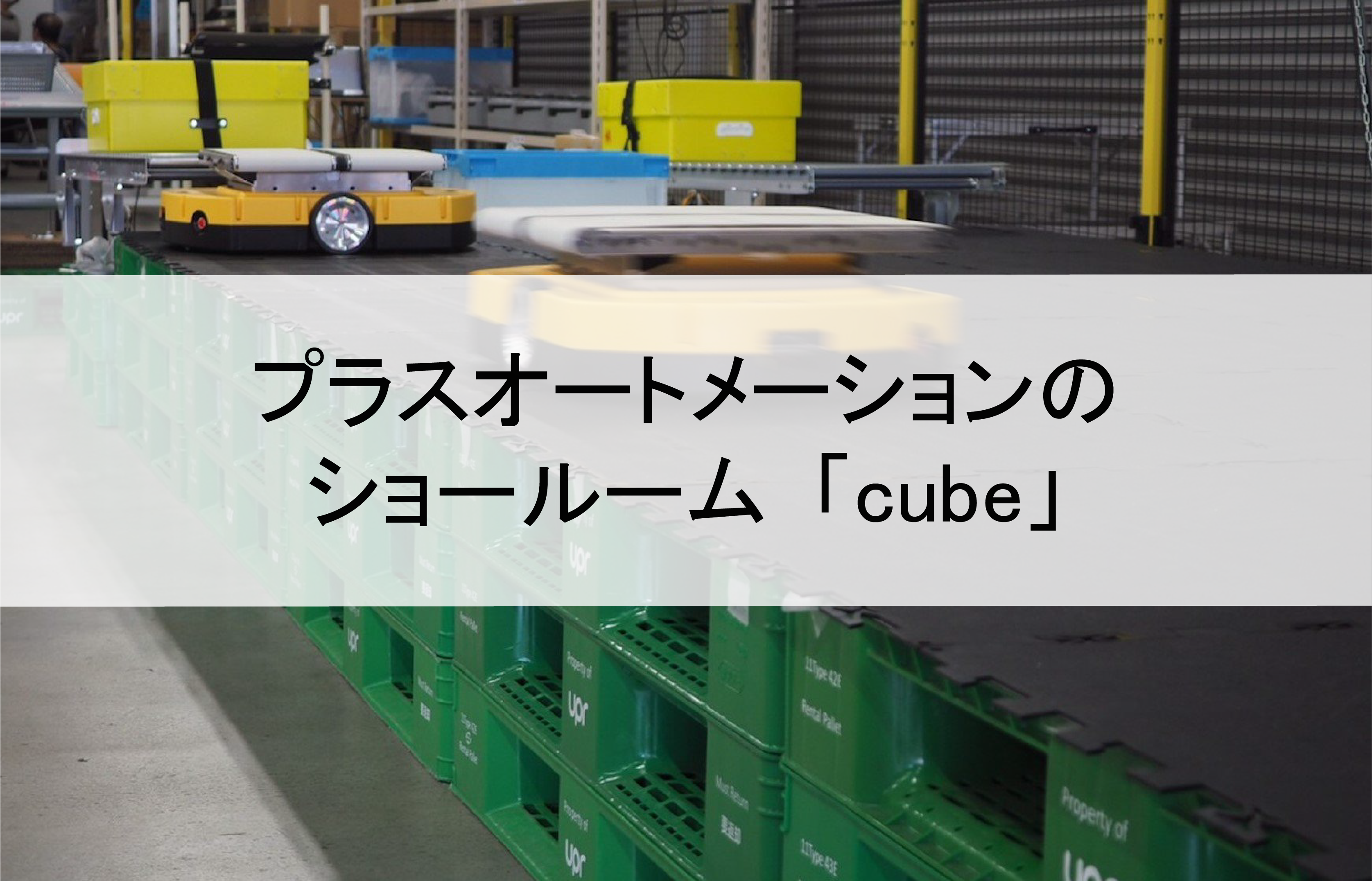
自社倉庫でも自動化を図りたいが、ロボットなどの導入するにあたって、どこから手を付けてわからないという方も多いでしょう。ですが、百文は一見にしかずと言われるように、インターネットで記事や動画を見るよりも、実際に見に行った方が、物流ロボットの有用性を実感しやすいはず!
そこで、物流ロボットの導入事業者へのコンサルティングから、最適なロボットとソフトウェアの導入・運用までを、月額定額制(サブスクリプション)で提供する、プラスオートメーションのショールーム「cube」へ訪ねてみた。
そこで見て感じてきた、物流ロボットの実力をレポートする。
目次: 1. ベルトコンベアを代替する以上の働きをする仕分けロボット「t-Sort」 2. 「t-Sort」シリーズの機能 3. ピッキング作業を高効率化する協働型ピッキングアシストロボット 4. 既存設備を活かしつつ、物流DX化を始める |
レポートに進む前に言っておきたいのは、「物流DX」の実現に必要なのは、超最先端で高価なロボットばかりではないこと。特に物流業においては、人間のように様々な作業に対応できるようなマルチタスクなロボットではなく、単純だけれど反復が必要な作業をロボット(機械)化するだけで、生産性を一気に向上できる可能性があるということだ。
プラスオートメーションのショールームは、東京都の大井競馬場前駅から徒歩5分くらいの場所にあります。広い敷地に大きな倉庫が並ぶ、その一区画が、ショールームとして使われています。
今回は、実際の機械(ロボット)が動く様子を見ながら、同社の経営企画部長の山田章吾氏に説明して頂きました。
1. ベルトコンベアを代替する以上の働きをする仕分けロボット
「t-Sort」
ショールーム内で目立つのは、「t-Sort」シリーズというロボットです。見た目は、ひと回り大きなロボット掃除機と言ったところ。「t-Sort」は、名前の通り、物を「選別したり仕分け」するロボットです。
本体上部にチルトトレイを採用した「t-Sort sd5」。
指定された場所に到達すると、チルトトレイが持ち上がり、荷物を下ろす。
例えば、倉庫にある物(箱など)を出荷するシーンを想像してください。箱には、出荷先を記したバーコードが貼られています。まず、「t-Sort」に乗せられた箱のバーコードが読み込まれ、即座に「t-Sort」が走り出します。走りだした「t-Sort」は、出荷先ごとに分けられたエリアで停まり、箱を下ろします。
指定された場所に到達すると、チルトトレイが持ち上がり、荷を下ろす。
山田氏は、個人がメルカリで宅配便の事業所へ商品箱を預けて、事業所が、都道府県や他地域の事業所別に荷物を仕分けるシーンを想像すると分かりやすいと言います。
個人が持ち込んだ箱は、都道府県や他地域の事業所別に仕分ける必要があります。仕分けるのが10エリアくらいであれば、人の手で運んでも容易に作業は終わります。 クロスベルトを採用した「t-Sort cb30」。最大秒速2mで走行する
しかし、もし都道府県別であれば47エリアに分ける必要があります。もしくは、チェーンの店舗別に仕分けるとなると数十から数百に仕分けていく必要があるでしょう。こうした作業を人が行う場合には、下記のような工程になります。
- 箱に貼られた宛先を確認する
- 箱を持って、宛先別のエリアへ運ぶ
- 宛先とエリアが合っているかを確認
- 箱を指定エリアに下ろる
- 元の場所へ戻る
1〜5までの作業の一つ一つに、数秒から数十秒の時間がかかります。一つの箱を処理するのに、数十秒以上、倉庫が広い場合には数分の時間がかかるはずです。
同じ工程を「t-Sort」を使った場合は、これらが自動で処理されていきます。人は、「t-Sort」が故障せずに動いているか、宛先別のエリアに運ばれた箱がはみ出したり崩れたりしていないかなどを確認するだけになります。
こうして宛先別に集められた箱は、トラックに積み、出荷されていくことになります。
2. 「t-Sort」シリーズの機能
前述で、「t-Sort」の大きさを表現するのに、ロボット掃除機を想像してほしいと記しましたが、「t-Sort」がどんな仕組みなのかといえば、ロボット掃除機の最先端の上位機ほど複雑ではありません。
「t-Sort」は、まず物を運ぶためにモーターを搭載し、4つの車輪を搭載しています。箱を乗せて運ぶことができるのです。
運べる荷物の大きさ、積載物寸法は38cm×31cm以内が理想です。運べる荷物の重さ、最大積載重量は、「t-Sort」の本体上部に搭載するチルトトレイまたはクロスベルトにより異なり、最大5kg〜30kgです。
バッテリー駆動なので、およそ4時間ごとに充電が必要になります。ただし、バッテリー残量が減ってくると、「t-Sort」は、自動で充電器に接続します。誰かが「t-Sort」の充電シフトを管理する必要がないのです。また充電器の電圧は100Vなので、極言すれば一般家庭やオフィスでも使えます。
「t-Sort」用の充電器。100Vの家庭用コンセントでも使用可
「t-Sort」は、無人搬送機「AGV(Automatic Guides Vehicle)」という種類のロボットです。名前の中の「Guides」というのは、あらかじめ決められたガイドやマーク、レールが必要ということです。
「t-Sort」の場合は、現場導入時に専用のラバー製シートを敷き詰めます。DIYショップで売られているジョイント型のフロアや人工芝を想像すると良いかもしれません。これら一枚一枚のシートが、レールであり、住所のようなものになります。1台ごとの「t-Sort」に「シートAまで直進したら左に90度転回して、シートBまで直進して90度転回、シートCで停止して、荷物を下ろす」といった指令を出します。
AGV型の「t-Sort」の優れている点は、最先端のガイド不要で自律して動く「AMR」よりも、圧倒的に導入コストを抑えられる点にあります。また導入コストに関しては、大型倉庫で利用事例の多いベルトコンベアよりも抑えられるうえ、ベルトコンベアよりも狭いエリアでも容易にシステム構築が可能です。
■ 自動搬送ロボットCarriRo
プラスオートメーションが扱う「AGV(自動搬送ロボット)」には、ほかに「CarriRo(キャリロ)」があります。一見、搬送用の台車のようにも見えますが、「CarriRo」も、決められたガイド(床に貼られたマーキング)の上を自動で走行します。
例えば、トラックで倉庫に運ばれてきた大きく重い荷物を、「CarriRo」の上に載せて、指定した場所へ自動で運ばせるのに適しています。
また、定期的に同じルートを走り続けて、倉庫で出てくる大量の資材・廃材を運ぶといった使い方もされています。キャスター付きのラックなどを牽引可能なので、一度で多くの荷や資材・廃材を運べるのです。 台車型の自動搬送ロボット「CarriRo(キャリロ)」
あらかじめ床に貼っておいた、ガイドとなるシールの辿って移動する
ガイドが必要のない、追従モードという機能を備えているのも特徴です。1人では運べない量の荷物を運ぶ際に、「CarriRo」を1台“連れていく”ことができます。自分のあとを追従させるのです。自分はもう一台の台車を押して荷を運び、「CarriRo」にも荷物を積んで追従させれば、2倍の荷物が一度で運べます。
完全に自律走行できるわけではありませんが、前方に障害物がある場合には、自動で停止します。例えば前方を人が横切る際には、危険を検知して止まるため、安全な運用が可能です。
3. ピッキング作業を高効率化する協働型ピッキングアシストロボット
ガイドが必要な「AGV(Automatic Guides Vehicle)」とは異なり、完全に自律して荷を運ぶのが「AMV(Autonomous Mobile Robot)」です。「自律走行搬送ロボット」と訳されることが多く、本格的に「ロボット」と呼べるでしょう。
プラスオートメーションでは、協働型ピッキングアシストロボット「ラピュタAMR」を扱っています。
「ラピュタAMR」は、最先端のロボット掃除機にも搭載されているSLAMを採用しています。難しいのですが、「SLAM」とは「Simultaneous Localization and Mapping」の略称です。自己位置推定と地図の作成を同時に行える機能を備えているということ。
SLAM機能を備え、自律走行が可能な協働型ピッキングアシストロボット「ラピュタ-AMR」
前述の「t-Sort」や「CarriRo」のように、床などにガイドを設置する必要がありません。例えば、スタッフを新規に採用した際、まずは倉庫や社内をぐるりと歩いて巡らせますよね。「PA-AMR」も、はじめに倉庫内の通路などを全て移動します。この際にマッピング……つまり地図の作成を行います。そして、常に自分が倉庫内のどこにいるかを把握しています(自己位置推定)。
また導入時には、どの棚のどの位置に、何があるかなどのデータを「ラピュタAMR」と共有します。すると、「これらの商品を集めてほしい」と指令を出せば、瞬時に移動しはじめて、巨大な倉庫でも商品のある棚の前に停まります。
ただし「ラピュタAMR」には、人間の“手”にあたる機能を持ちません。そのため、指定した商品を人が「ラピュタAMR」の上に乗せていきます。
搭載するディスプレイに、人が向かうべき場所(ピッキングする商品の置き場所)を表示する。
「ラピュタAMR」が人が向かうべき場所を、明確に示してくれる。
これまで人だけで行っていたピッキング作業では、どの棚の何段目にどの製品が保管されているかを、作業員に学習させる必要がありました。ピッキング作業にも、熟練するスタッフが必要だということです。「ラピュタAMR」は、導入後の数時間後には、熟練スタッフと同様に、全ての製品の位置を把握できるということです。そして「ラピュタAMR」の提示する場所へ、人が移動してピッキングして載せればよくなります。
マッピングや自己位置把握のために、各種センサーを搭載。
人などの障害物も検知し、危険な場合は停まったり回避したりする
4. 既存設備を活かしつつ、物流DX化を始める
山田氏は、同社が担う役割を次のように語ります。
「物流は、海外から商品が出荷されて、日本の港まで運ばれてきて小口に分けて倉庫に入れ、商品の売れ行きに合わせて倉庫から出荷されていきます。そうしたなかでプラスオートメーションが担当しているのは、倉庫の中での商品の流れに関わっています。
その倉庫内を振り返れば、商品が入ってきて、それを保管する、保管した商品を徐々に出荷していくという3段階の作業があるとします。3段階に工程を分けた場合に、プラスオートメーションの提供サービスが活躍するのは、保管した商品を徐々に出荷する際のピッキングや仕分けです。
以前は、倉庫と言えば、パレットごとに入荷と出荷を繰り返していました。でも昨今では、ネットショップなどのECの普及などがあり、1箱プラス1ピースなどの単位で出荷されることも多いです。箱ごと出せば良いという物流よりも、複雑化しているんです。そのため、以前は大掛かりな機械を使っていましたが、より小回りの効く機械やロボットが求められているんです。」
物流ロボットにも様々な種類がラインナップされています。プラスオートメーションでは、まず導入を考えている事業者に、どのような自動化を求めているかヒアリングします。できるだけ既存の設備や倉庫管理システム(WMS)を活かしたシステムと、それに必要なロボットを提案します。
ヒアリングから1カ月後、現場のシステム構築をはじめてから1週間後には、新たな物流システムを構築できると言います。
例えば「t-Sort」であれば、ラックの上にシートを敷くことでも、運用できる。
既存設備も最大限に活かせるのだ
---
現状、国内の物流業界では、人件費が安価な割に、優秀な人材が集められている事業者が、少なくありません。また、倉庫管理システム(WMS)などを含め、システムの最適化がきちんと図られている現場も多いです。だが日本では少子化が進んでいるなどが原因で、近い将来に必ず、人材確保が難しくなります。今後は、物流倉庫の自動化は、避けられない状況なのです。
もちろん倉庫内すべての自動化は、ハードルが高いです。そこで、既存設備やスタッフを活かしつつ、できるところから自動化を進めていくことが重要です。まずはプラスオートメーションの「Cube(キューブ)」など、ショールームに足を運んでみてはいかがだろう。物流DXへの理解が、一気に進むことと思います。