【物流用語】誤出荷とは?8つの対策法や原因・影響について詳しく解説
誤出荷は顧客との信用問題に関わる重大な過失です。発生した時点で原因を究明して対策を考えるべきですが、どのような対策が必要なのか分からない企業も多いのではないでしょうか。 そこでこの記事では、倉庫での誤出荷を改善するために有効な対策を紹介します。誤出荷が発生する原因や影響についても解説しますので、ぜひ最後までご覧ください。
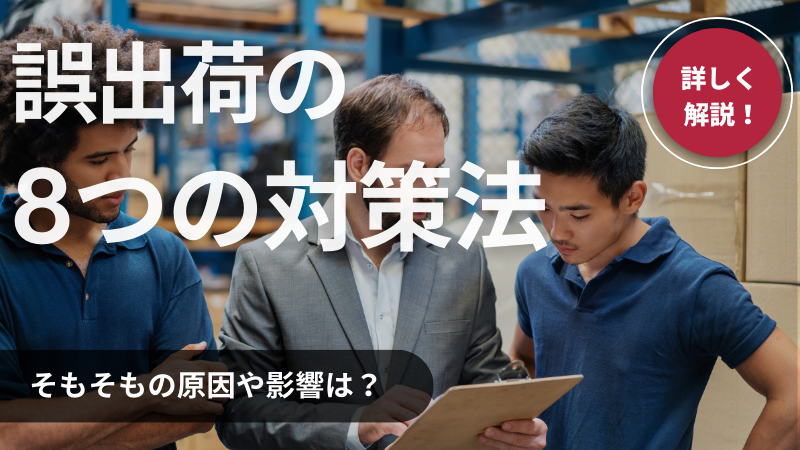
1.誤出荷とは?
誤出荷とは出荷する商品の種類や数量、また発送先などを間違えてしまうことを指します。誤出荷が発生すると顧客との信用問題に関わるため、発生しないような仕組みづくりが非常に重要です。
誤出荷の発生を表す指標として、「誤出荷率」があります。これは、作業件数におけるミスの発生割合を表す数値で、以下の式から求めることができます。単位はPPM(Parts Per Million)です。
例えば、出荷受注数が100個で誤出荷件数が10個の場合、誤出荷率は0.1になります。
2. 誤出荷が与える4つの影響
誤出荷はさまざまな影響を及ぼすことも理解しておく必要があります。
- 個人情報の漏洩問題
- 顧客との信頼関係の悪化
- 在庫に差異が生じる
- 余計なコストがかかる
どれも大切なことなので目を通しておきましょう。
2-1 個人情報の漏洩問題
送り先を間違えるという誤出荷は、あってはならない物流事故です。相手の納品伝票が入っていれば、個人情報の漏洩問題に直結します。
特にECサイトは個人のお客様への配送がほとんどであるため、より事態は深刻です。個人情報を悪用されるケースもないとは言い切れません。
2-2 顧客との信頼関係の悪化
誤出荷は顧客との信頼関係に直結します。大きなトラブルにつながるような誤出荷であれば、今まで築き上げた関係が一気に崩れてしまうかもしれません。
また、商品をブランドから委託されて出荷している場合、ブランドイメージを大きく損なう可能性もあります。信頼関係の構築には時間がかかりますが、崩れるのは一瞬です。
2-3 在庫に差異が生じる
異なる商品や数量違いで誤出荷となった場合、在庫に差異が生じます。送り間違えた商品はどれなのか、何個間違えてしまったのか、きちんと状況を把握して在庫数を調整しなければなりません。
ときには大量の伝票の中から該当するものを探し出す作業が必要です。イレギュラーな作業が発生することで、作業効率が大きく低下します。
2-4 余計なコストがかかる
誤出荷の商品を返品してもらい、正しい商品を送り直すことで、予定外の配送費用がかかります。さらに発送手配やお客様への謝罪、原因究明などで人件費もかさむでしょう。
誤出荷によるイレギュラーな費用は、できれば避けたい物流コストです。大きなトラブルに発展すれば、慰謝料を求められるケースもあります。
3. 誤出荷の改善に有効な対策を8つ紹介
こちらでは、誤出荷の改善に有効な8つの対策を紹介します。
|
3-1 作業手順やルールを明確にする
作業手順やルールを定め、マニュアルとして誰でも見やすいようにしておきましょう。作業手順が統一されれば、万が一誤出荷が起こった際に原因が特定しやすくなります。
入荷・出荷・荷役・流通加工など、あらゆる手順をマニュアル化しておくと安心です。新人教育もしやすくなります。
特に出荷に関わるルールは定期的に見直すことが大切です。ハンディターミナルの使い方や不良品の基準など、文章で伝えにくい部分は写真を用いたマニュアルにすると作業者が判断しやすくなります。
3-2 ロケーションを見直す
間違えやすい商品がある程度決まっているなら、ロケーションの見直しも必要です。似ている商品は離しておく、間違えないように印を付けておくなどの対策をとりましょう。
また、コスメや雑貨などの細かい商品を取り扱う場合、隣り合う商品同士が混ざらないように管理することも重要です。色違いやフレーバー違いなど、ラインナップが多い商品ほど取り違えないための対策を整えておきましょう。
3-3 整理整頓を心がける
倉庫内の整理整頓を心がけ、十分な作業スペースを確保することが大切です。テーブルには必要なものだけを置き、1出荷分ずつ検品・梱包を行えば、商品や送り状が混ざる心配はありません。
作業に携わる人数が多いほど、1人あたりの作業スペースが少なくなります。ピッキングと検品で担当者が分かれる場合は、きちんと置く場所や流れを決めて商品が混ざらないように注意しましょう。
3-4 誤出荷の原因を究明する
誤出荷が発生した際は早急に原因を究明し、再発しないための対策を練ることが重要です。大きな問題にならなかったからといって、ただのミスで終わらせてはいけません。
また、誤出荷にはさまざまな原因があることを紹介しましたが、その背景には作業者の心理状態や作業環境が関わっている場合もあります。
- 違和感があったけど自己判断で出荷してしまった
- ピリピリした雰囲気が怖くて聞けなかった
- 早く終わらせたくてチェックが適当になっていた
- 商品の区別が分かりにくいものをそのままにしていた
倉庫環境を改善するとともに、現場の雰囲気や作業者の意識を改善することも必要です。
3-5 情報共有を徹底する
誤出荷が起きた状況や原因などの情報を、作業者全員に伝えることが大切です。事の重大さが分からなければ、ひとりひとりの意識はなかなか変わりません。
作業に変更点がある場合は、誰もが見える場所に分かりやすく記しておきましょう。従業員が多い倉庫では、ひとりひとりに情報共有できる仕組みを整える対策も必要です。連絡事項を確認したらサインを入れてもらうなど、管理しやすい方法が良いでしょう。
3-6 倉庫管理システム(WMS)の導入
手作業による誤出荷が多い倉庫なら、倉庫管理システム(WMS)の導入が有効です。在庫管理やロケーション管理など、倉庫内の運営をサポートし、最適化を実現できます。
システムを用いて検品することで、商品違いや数量違いにすぐ気付ける点がメリットです。なかには賞味期限を管理できるタイプもあり、出荷前の見落としを防げます。
さまざまなタイプのシステムがあるので、取り扱う商品に適したものを選びましょう。
3-7 アウトソーシングを検討する
誤出荷がなかなか減らないことが大きな悩みであるなら、アウトソーシングも検討してみるのも1つの方法です。プロに委託することで誤出荷の悩みから解放され、その分ほかの業務に専念できます。
アウトソーシング先を探す際は、自社商品と同様の商品を取り扱っている倉庫であると安心です。実績や拠点、対応力などを確認して選びましょう。
3-8 出荷作業の自動化を検討する
誤出荷の数をグッと減らしたいのであれば、出荷作業の自動化が有効です。出荷作業の一部をロボットに任せることで、誤出荷を削減し、作業効率も改善します。
近年では物流倉庫の自動化が進み、ロボットを導入する倉庫が増えつつあります。倉庫の人手不足を改善する手段としても効果的です。
ロボットは導入コストがかかると思われがちですが、当社プラスオートメーションでは初期費用ゼロ、月額使用料のみのシンプルな料金体系でロボットを提供しています。出荷をサポートするロボットを2種類紹介しますので、ぜひ参考にしてみてください。
次世代型ロボットソーター「t-Sort」
t-Sortは、仕分け作業をサポートしてくれるロボットソーターです。方面別・オーダー別・店舗別の仕分けをスムーズに行い、最大30kgまでの商品を運搬できるのが特徴です。物流ロボットとして次のような特長があり、購入とサブスクリプション形態の2種類から利用形態を選べます。
・最短1日からのスピーディな導入
・ソーター比約1/3~1/2の省スペース性
・既存のレイアウトにも柔軟に導入可能
次世代協働型ピッキングロボット「ラピュタAMR」
ラピュタAMRは、ピッキング時の運搬をサポートする自律走行可能なロボットです。レーザーによる障害物検知機能が付いており、人と接触する心配がありません。
初心者でも操作しやすい設計になっていますので、誰でも同じ手順で出荷作業を行えるのがメリットです。ピッキング時の移動にかかるタイムロスも削減できます。
4. 倉庫で多い誤出荷とは?そもそもの原因5つを解説
倉庫で発生する誤出荷は、主に5つに分類にできます。それぞれ起こりうる原因を知ることで、取り組むべき対策が見えてきます。すべて確認しておきましょう。
|
4-1 商品内容の違い
商品内容の違いは、発注した商品と異なる商品が届くことです。
- サイズ違い
- カラー違い
- ロット違い
- フレーバー違い
- 新旧商品の違い
システムやロボットによる出荷サポートを行っていない倉庫ほど、商品を取り違える可能性が高くなります。誤出荷が発生した時点できちんと原因を究明することが大切です。
- 出荷時に取り違えてしまった
- 入荷時に棚入れする場所を間違えた
- 流通加工時にラベルを貼り間違えた
上記のように、取り扱う商品によってさまざまな原因が考えられます。どの作業が原因で誤出荷につながったのかを把握することが重要です。
4-2 商品数量の違い
商品数量の違いは、発注した商品の数と届いた商品の数が一致しないことです。商品内容の違いで解説した原因と同様で、目視のみのチェックであるほど間違いに気付かないまま出荷する可能性が高くなります。
数量を間違えてしまう理由には、以下のような原因が考えられます。
- 単純な数え間違い
- 入り数の確認不足
- バラとケースの取り違え
- ハンディターミナルの操作ミス
- 流通加工時のセットミス
なかには商材の特性で商品同士がくっつきやすいものもあります。冬場であれば静電気による影響もあるでしょう。
ハンディターミナルを用いて検品していても、手順がルール化されていないと見落としは防げません。
4-3 送り先の違い
A店に送るはずの商品をB店に送ってしまうなど、送り先の違いはもっとも避けたい誤出荷です。以下のような原因が考えられます。
- 似たような店舗名を見間違えた
- 複数の商品をテーブルに置き、梱包時に送り状が混ざってしまった
- 梱包後に送り状を発行し、同じ個口数の送り状を逆に貼ってしまった
- マスタ登録する際に入力を間違えた
- 手書き伝票に異なる住所を記載してしまった
手順がルール化されていない場合や、管理が徹底されていない場合に起こりやすいミスです。チェック体制を整えるだけでも見落としは減るでしょう。
倉庫で取り扱う商品の中には、商品サイズがバラバラで、個口数が確定してからでないと伝票発行できないものもあります。似たような店舗名を貼り間違えてしまうことも多いので、思い込みによる貼り間違えに注意しましょう。
4-4 同梱物の入れ忘れ
ひとまとめに同梱物といっても、その種類は多岐にわたります。
- 商品の付属品
- ノベルティ
- ブランドのショップ袋
- 条件付きのプレゼント
- ショップの販促物
入れ忘れを防ぐためにはバーコード管理が有効ですが、商品によっては難しいものもあります。単純な入れ忘れだけでなく、作業者への伝達漏れによって発生する可能性もあるので注意が必要です。
特にECサイトではさまざまなノベルティ企画があり、時期や条件によって内容が変化します。すべての作業者が分かりやすい仕組みを整えることが重要です。
4-5 検品不足商品の出荷
正しい商品が届いても、使えなければ意味がありません。検品不足による見落としが誤出荷の原因です。
- 破損品の見落とし
- 汚れの見落とし
- 異物混入や沈殿物の見落とし
- 賞味期限、消費期限、使用期限の見落とし
例えば賞味期限であれば「期限の〇日前までなら出荷可能」といった基準が設けられています。また、沈殿物が発生しやすい化粧品や食品などは「どの程度までなら出荷可能」といった基準が決められているものも多いです。
出荷基準を見落として商品を発送してしまうと、顧客に不信感を与えてしまいます。
5. 自動化も検討しながら誤出荷を抑えよう
誤出荷を改善するためには、しっかりと原因を究明し、対策を整えることが重要です。たった一度の誤出荷が大きなトラブルに発展し、顧客との信頼関係に影響する可能性があります。
プラスオートメーションでは、倉庫の自動化に関するご相談をお受けしています。
|
など、お悩みやご不明な点がありましたら、下記のフォームよりお気軽にお問い合わせください。