ピッキング作業のよくあるミスと原因、7つの改善策を紹介
ピッキングミスは、顧客との信頼関係に直結します。たった一度のミスで、今まで築いてきた信頼関係が崩れてしまうかもしれません。そこで本記事では、ピッキング作業でミスが発生する原因を解説するとともに、ミスをなくすための改善策を7つ紹介します。すぐに取り組める施策もありますので、ぜひ最後までご覧ください。
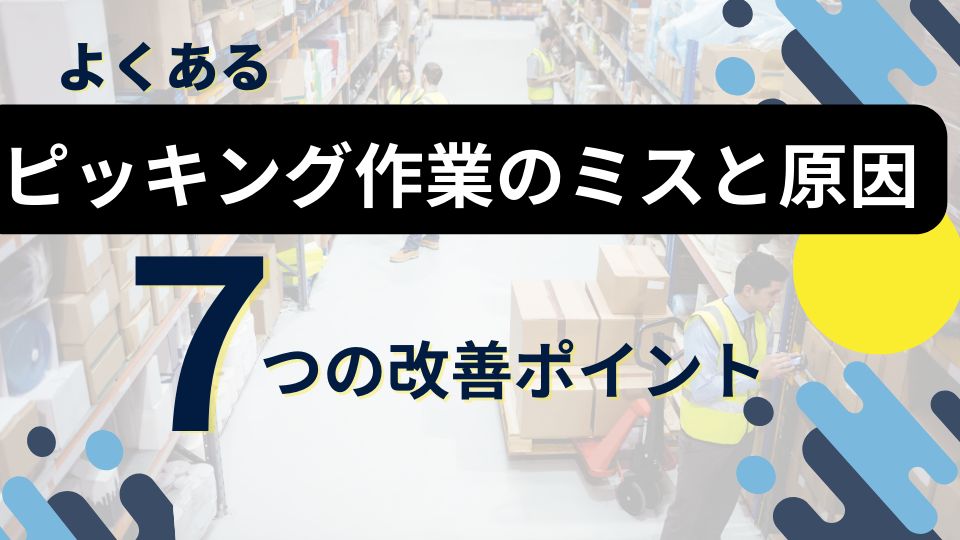
1. ピッキングは2種類
ピッキングには、大きく分けて次の2種類の方法があります。それぞれ解説します。
|
1-1 摘み取り式(シングルピッキング)
「摘み取り式(シングルピッキング)」は、オーダー単位のピッキングリストごとに商品のある場所まで移動するピッキング方式です。多品種少量の商品を取り扱う場合に適しています。
EC・通販事業の膨大な発注に適しているのも摘み取り式です。商品を集めてから検品・梱包・出荷までを1つの作業単位で完結できるので、指示を受けてから出荷完了までのスピードが早く、間違いがあった場合にもすぐに修正することが可能です。
1-2 種まき式(トータルピッキング)
「種まき式(トータルピッキング)」は、その日の出荷に必要な商品を先にまとめてピッキングする方式です。商品の種類が多くはないが、1商品あたりの数量が多く、納品先が特定数に決まっている場合に適しています。
ピッキングリストごとに何度も動き回る必要がありませんが、検品・梱包のスタートには時間がかかります。
種まき式は最初にまとめてピッキングした商品を置く場所と、各納品先へ仕分ける場所の確保と仕分ける時間がかかります。
2. ピッキング作業で起こりやすい4つのミス
ピッキング作業で起こりやすいミスの種類を4つ紹介します。それぞれ確認しておきましょう。
|
2-1 商品内容の違い
商品内容の違いは、発注した商品と異なる内容が届くことです。具体的には以下のようなケースがあります。
- サイズ違い
- カラー違い
- 品番違い
- 新旧商品の違い
これらはピッキング時の商品の取り違えで起こることがほとんどです。例えば25.5cmの靴を頼んだのに25cmが届いた、NV(ネイビー)を頼んだのにNA(ナチュラル)が届いたなど、似たような商品を間違えてしまうことも多くあります。
目視での検品を行っている倉庫で、このような取り違えが多く発生しがちです。
2-2 商品数の違い
商品数の違いは、発注した数と異なる数量で届くことです。ピッキング時の原因として、以下のようなミスが考えられます。
- 入り数の確認不足
- バラとボールとケースの取り違え
- ハンディターミナルの操作ミス
例えば同じ商品を5ケース出荷しなければならない場合、ハンディターミナルで1ケースずつ検品を行えば数量を間違えることはありません。しかし、1ケースだけ検品して数量を「×5」と入力してしまうと、実際は4ケースしかないのに検品だけが問題なく完了してしまう可能性があります。
2-3 賞味期限の確認もれ
賞味期限のある商品を送る際は「賞味期限から○日間前までなら発送可能」などのルールがあります。消費期限や使用期限の場合も同様です。
この基準をしっかりと確認せずに発送してしまい、クレームにつながることがあります。万が一賞味期限切れの商品が発送されたとなれば大問題です。
BtoBの場合、同じ商品でも「○日前まで」という基準は発送先によって異なる場合があります。食品や使用期限のある商品を取り扱う倉庫では、徹底した管理力が必要です。
2-4 同梱物の入れ忘れ
特にECサイトの場合、ショップ専用の袋やノベルティなど、さまざまな同梱物が発生します。最初から商品にセットしておくことで入れ忘れを防げるものもありますが、特定の条件で発生するプレゼントなど、ピッキングリストを確認して入れなければならないものもあるので注意が必要です。
例えば「プロテインを○日までに購入した方にシェイカーをプレゼント」など、期限付きで同梱物が発生するケースもあります。さまざまな作業者がピッキングを行う倉庫では、「知らなかった」という事態が起こらないように情報共有を徹底しなければなりません。
3. ピッキング作業でミスが発生する2つの大きな原因
ピッキング作業でミスが発生する原因は、大きく分けて2つあります。
- 作業ルールが徹底されていない
- ロケーション管理が徹底されていない
ピッキング時のミスが減らないことで悩んでいる事業者は、思い当たる部分がないか確認してみましょう。
3-1 作業ルールが徹底されていない
ピッキング作業は慣れてくると自分のやり方(属人的)になりがちです。ピッキング時に起こるミスの多くは、作業ルールが徹底されていないことが大きな原因とも言えます。
- 商品の取り出し方
- 検品のタイミング
- ハンディターミナルの操作方法
ピッキング作業に関わるこれらの手順がルール化されていないと、どの段階でミスにつながったのかも分かりません。新人教育時には、教える人によってやり方が異なるといった事態も発生します。
ハンディターミナルを用いてピッキングをする場合、商品を取り出しながら検品まで行うやり方と、商品を一通り揃えてから検品をするやり方があります。取り扱う商品に適したやり方で作業ルールを徹底しましょう。
3-2 ロケーション管理が徹底されていない
ロケーション管理をしていても、整理整頓ができていなかったり、あるはずの場所に保管されていなかったりしたら意味がありません。ロケーション管理が徹底されていないことでミスにつながる可能性があります。
類似商品が複数並んでいる場合は、隣合う商品と混ざらないように仕切りを入れるなどの対策が必要です。パッと見て商品の違いがすぐに判断できるようにしておくと良いでしょう。
ピッキングをする際にやりにくさを感じているのであれば、ロケーション全体の見直しが必要です。
4. ピッキング作業でミスを防ぐための7つの改善策
ピッキングミスに気付かないまま出荷をしてしまうと、顧客からの信用を失います。さらに、原因の追求や報告書の作成などといった作業が発生するでしょう。
そうならないためにも、ピッキング作業でミスを防ぐ対策が必要です。こちらでは、7つの改善策を紹介します。
- 作業マニュアルの作成
- ロケーションの見直し
- ピッキングリストを見やすくする
- 同梱物をバーコードで管理する
- 必要な情報が全員に伝わる仕組みを整える
- 倉庫管理システム(WMS)の導入
- ピッキング作業の自動化
自社の状況を把握し、できることから始めてみましょう。
4-1 作業マニュアルの作成
作業マニュアルを作成することで、誰でも同じようにピッキング作業ができるようになります。新人教育の際に「教える人によってやり方が違う」という事態にもなりません。
マニュアルを作成する際は、ハンディターミナルの操作手順や不良品の基準も明確にしておきましょう。返品がともなう商品は返品作業のルール化も必要です。
言葉だけだと分かりにくい部分は写真を入れることで伝わりやすくなります。自己流のやり方にならないように、定期的に見直す習慣作りが大切です。
4-2 ロケーションの見直し
あまりにもピッキングミスが多いのであれば、そもそもロケーションが適切であるのかという点から見直す必要があります。商品が棚から溢れている場合や、隣り合う商品ときちんと仕切られていないのも改善すべきポイントです。
類似商品によるミスが多いなら、取り違えやすい商品を離して管理するなどの対策も有効です。作業効率や出荷頻度を考慮し、作業者がピッキング時に悩まないようなロケーション作りをしましょう。
4-3 ピッキングリストを見やすくする
ピッキングリストは必要な情報だけを見やすく記載することが大切です。余計な情報が増えると品番や数量を見間違えてしまう可能性があります。
ピッキングリストに記載する必須項目は以下の3つです。
- ロケーション
- 品番
- 数量
文字を大きくしたり、色やデザインを工夫したり、何行目を見ているのかを判断しやすいと良いでしょう。作業効率を重視したピッキングリストが望ましいです。
4-4 同梱物をバーコードで管理する
同梱物の種類が多いほど、入れ忘れにつながる可能性があります。すべてを記憶することは難しいため、バーコードで管理する方法が有効な施策です。
同梱物自体にバーコードを貼付できなくても、ピッキングリストにバーコードが表示されることで同梱物の有無に気付けます。
4-5 必要な情報が全員に伝わる仕組みを整える
業務の変更点や起こったミスなど、必要な情報が作業者全員に伝わる仕組み作りが重要です。
出勤日数や出勤時間は人によって異なります。重要な連絡事項を朝礼や昼礼で伝えるだけでは全員に伝わりません。また、ローテーションで複数の仕事を受け持つ場合、特定の作業に時々しか携わらないこともあります。
細かい変更点やミスが多い部署は、作業開始前に必ず業務連絡書を確認してサインをするなどの対策を整えておくと良いでしょう。一人ひとりが確認したことを判断しやすくなります。
特に重要な連絡事項は、全員が目を通すホワイトボードや該当商品がある場所に明記しておくと安心です。
4-6 倉庫管理システム(WMS)の導入
倉庫管理システム(WMS)は、倉庫内の運営をサポートし、最適化するサービスのことです。入出庫管理や在庫管理などを行い、倉庫状況を把握しやすくなります。
SKUが多く、管理が複雑な商品であるほどWMSの導入が有効です。業務の効率化やコスト削減につながります。
蓄積されたデータで倉庫の現状を把握し、問題点を洗い出すことも可能です。WMSにはさまざまな種類がありますので、自社商品の管理に適したシステムを選択しましょう。
4-7 ピッキング作業の自動化
ピッキング作業のミスを防ぐためには自動化も有効です。近年では物流倉庫の自動化が進み、ピッキング作業をサポートするロボットを導入するケースも増えています。
ピッキング作業をロボットに任せることで、ヒューマンエラーを大きく改善できます。人手不足に悩む倉庫であれば、省人化・省力化につながる取り組みとしても効果的です。
物流ロボットのサブスクリプションサービス(RaaS)を展開する当社プラスオートメーションでは、ピッキング作業をサポートするロボット「ラピュタAMR」を提供しています。
ラピュタAMRはピッキング時の運搬をサポートするロボットであり、自立走行で人との協働が可能です。誰でも操作しやすいUI設計となっておりますので、人によってやり方が異なるという問題もありません。
「ロボットは導入コストがかかるから難しい」という事業者様は、当社のRaaSを活用することもご検討ください。初期費用ゼロ、月額定額制でご利用いただける安心のサービスです。ご不明な点がございましたら、お気軽にお問い合わせください。
5. まとめ
ピッキング作業時のミスが多い倉庫は、早急にミスを防ぐ対策を整えることが重要です。たった一度のミスで今まで築いてきた顧客との信頼関係を失うかもしれません。
ピッキングミスのほとんどは、作業ルールやロケーション管理が徹底されていないことが原因です。倉庫環境を見直し、できるところから改善していきましょう。
プラスオートメーションでは、ピッキング作業時のミスを改善するためのご相談もお受けしています。「ミスがなかなか減らない」「マニュアルが定まらない」など、お悩みや心配ごとがありましたら、下記のフォームよりお気軽にお問い合わせください。