【事例あり】ピッキング作業の課題と改善法を詳しく解説
ピッキングは、出荷の上流工程にあり速さと正確性、庫内標準作業を遵守する精神が求められる作業です。本記事では、ピッキング作業でよくある課題について解説するとともに、効率化する方法をご紹介します。記事の最後ではロボットを用いた改善事例も紹介していますので、ぜひ最後までご覧ください。
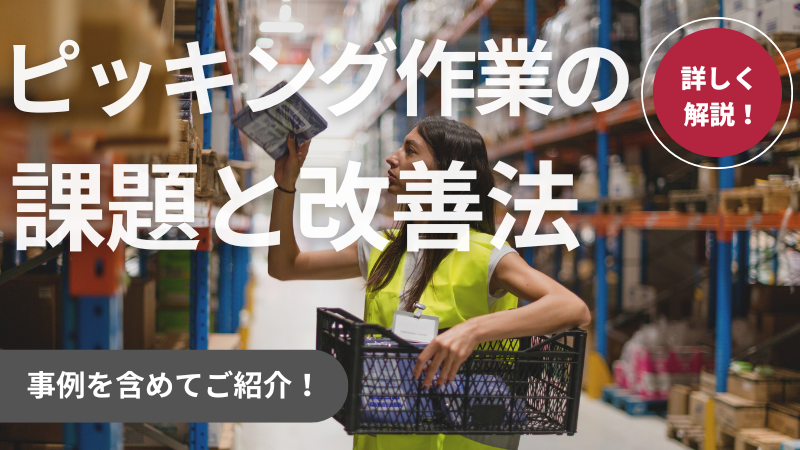
1. 物流倉庫におけるピッキング作業の4つの課題
作業の改善策を考える前に、どこに、どのような課題があるのか細かく洗い出すことが大切です。こちらでは、物流倉庫におけるピッキング作業のよくある課題を4つ紹介します。
- ピッキングミスが発生する
- 商品を探すまでに時間がかかる
- 商品棚までの移動に問題がある
- 商品の取り出しに時間がかかる
1-1 ピッキングミスが発生する
ピッキング作業で発生しやすいミスは次の3つです。
- 商品違い
- 商品数量の違い
- 付属品忘れ
どんなに注意していても人間が作業をしている以上、なかなかミスをゼロにすることはできません。特にハンディターミナルなどの機械的な管理ができていない倉庫ほど、ピッキング時の間違いに気付けず、ミスが起こりやすくなります。
なお、ピッキングに限らずオペレーションミスが発覚した際は、きちんと原因究明をすることが大切です。単純な間違いが原因なのか、倉庫環境に問題があるのかなど、原因を明らかにして同じミスを繰り返すリスクが高くなります。
ヒューマンエラーである、と結論付ける事は最終手段とした上で、ミスの5W1Hを整理し、正しく分析した上での原因究明をお勧めします。
1-2 商品を探すまでに時間がかかる
いくらロケーション管理されている倉庫でも、商品を探すまでに時間がかかっていたら非効率的です。下記の内容がないかチェックしてみましょう。
- 保管場所が分かりにくい
飛び地のようになったロケーションがありませんか? - ピッキングリストが読みにくい・商品番号が確認しにくい
オペレータが必要としている情報が順番に読み取れるようになっていますか?
商品に商品番号(JANコード)はどのように記載されていますか? - 保管場所が間違っている
商品格納時のミスが発生していませんか?ミスピック後の戻し先ミスの発生は? - ロケーション番号が分かりにくい
よく見る定型に則っていて、本来その現場に必要な情報レベルにまで整理されていますか?
そもそもロケーション管理されていない倉庫では、特定の人しか分からない状態になっている可能性が高いでしょう。誰もがピッキングしやすい状態でなければ、生産性は改善されません。
1-3 商品棚までの移動に問題がある
ピッキング時の導線を見直し、ロケーションまでの移動に問題がないか確認しましょう。
- 出荷頻度の高い商品の格納場所が奥まっている
- 通路が狭くて台車が通れない
- 特定のロケーションに人が集中してピッキング待ちが発生する
- 作業導線を考慮した設計になっていない
- 歩行ルートをオペレータに考えさせている
このような状態だと、ロケーションへたどり着くまでに時間がかかります。無駄な歩行や待ち時間、考えて判断に費やす時間が、ピッキング作業の効率を低下させている原因です。
1-4 商品の取り出しに時間がかかる
ピッキング時に必要な商品をすぐに取り出せないと、タイムロスが生じます。具体的には以下のような状況です。
- 商品を1個取り出すために大きい箱を開けなければならない
- 引き当てのかかる在庫と、補充用の在庫の格納先が同一になっている
- 棚の間口に対して商品が大きい、もしくは長い、極端に重い等の要因で取り出しにくい
- 開口部が作業者のほうを向いていない
- 先入れ先出しや賞味期限を判断しにくい
- フォークリフト等の専用機器を使用しないと取り出せない
例えば小さな商品が入荷した際、200個入りなどで外箱が大きく、かつケースの中でボール単位になっている場合があります。さらにその商品の出荷形態が、ケース、ボール、バラ、全てに対応している上に、JANコードも共通・・・となった場合、そのままの状態で保管してピッキングを行うと、毎回ケースから必要数を取り出すために認知と判断の手間が発生します。
こういった場合は入荷の時点でそれぞれに異なるハウスコードを貼付する事でピッキングオペレーションは改善されますが、その一方で入荷と格納オペレーション、在庫管理が煩雑になります。このように、倉庫現場では一筋縄ではいかない苦労をされている事でしょう。
2. ピッキング作業を効率化する5つの方法
こちらでは、ピッキング作業を効率化する方法を5つ紹介します。
- 倉庫のレイアウトを見直す
- ピッキングリストを見やすくする
- トータルピッキングを採用する
- ピッキング作業を標準化する
- ピッキング作業を自動化する
2-1 倉庫のレイアウトを見直す
ピッキング時の歩行導線を考えたレイアウトにし、ロケーションあたりに格納するSKU数を制限する事で商品を見つけやすい状態を保てます。また、間違えやすい商品は同一ロケーションに格納しないという工夫をしましょう。出荷頻度の高い商品は、次工程に近いエリアに纏めて格納しておく事で歩行を減らす事が出来ます。
また、人がすれ違うためのスペースを確保し、通行の妨げがないようにすることも見直すときのポイントです。保管効率を考慮すると通路が狭くなりがちですが、それによってピッキング効率が低下するリスクも考えなければなりません。
2-2 ピッキングリストを見やすくする
ピッキングリストに最低限必要な情報は以下の3つです。取り扱う商材によっては賞味期限やロットNo.等、必要な情報が増えていきます。
- ロケーション番号
- 商品番号(JANコード)
- 数量
必要な情報以外を表示させないようにし、ピッキングリストを見やすくすることで効率化につながります。目に入って来る情報の並びの整理や、ロケーション番号や数量など、重要な情報は文字を大きくする工夫も有効です。
ピッキングリストに不要な情報が書かれていたり、情報の記載順序がバラバラで読み辛かったり、文字が小さかったりすると、認知を誤る可能性が高まるので注意しましょう。
さらにピッキングリストに載る商品の順番は、最短ルートでピッキングが完結できる並びであることが理想です。最短ルートと一口に言っても、ロケーションを順番に記載した所で実際に歩くルートを選択するのは人間です。従って、ロケーション間の歩行ルールの確立も同時に確立することで、商品を探すまでの時間が改善されます。
2-3 トータルピッキングを採用する
トータルピッキングとは、オーダーを受けた商品をまとめてピッキングし、その後に工程を分けて、仕分けを行ってから出荷する方法です。
注文が入った商品をまとめてピッキングするので、作業者の移動する時間を短くしたり、商品を探す時間を削減したりできます。
また、ピッキング→検品仕分け→出荷時検品→梱包と、二重で検品を行う工程を組めるため、出荷ミスの防止にも効果的です。
基準は様々な要素に左右されますが、主に1出荷あたりのピース数が2以上5以下程度で、出荷件数の多い倉庫にとって、トータルピッキングは有効な手段だといえます。
2-4 ピッキング作業をルール化する
ピッキング作業をルール化することで、ミスの軽減につながります。ルールが定まっていないと作業者によって手順が異なり、何が原因でミスが発生したのかを究明しにくくなります。
例えばハンディターミナルを用いて作業していても、手順が統一されていないとミスが起こる可能性があります。
例えば商品が5個必要なのに4個しかピッキングしなかった場合、1個ずつバーコードを読み取っていれば不足に気付けますが、「×5」と入力してしまうと間違いを把握できません。
また、作業のルール化は新人教育時にかかる時間の削減にもつながります。マニュアルを作成し、作業者がいつでも見られるようにしておきましょう。
2-5 ピッキングを補助するロボットを導入する
効率化する方法として、ピッキング作業を補助するロボットの導入も有効な方法の1つです。作業者の歩行負担が改善するだけでなく、現場によっては効率の改善も見込め、ミスの軽減や人件費の削減にもつながります。
人手不足で悩む倉庫ほど、自動化や人を補助するロボットの導入を検討しましょう。人手不足は今後さらに深刻化していくとされる問題であり、早めの対応が必要です。
なお、当社プラスオートメーションでは、次世代協働型ピッキングロボット「ラピュタAMR」を月額定額制で提供しています。初期費用がかからないため、導入コストで悩む心配がありません。
ラピュタAMRは、商品の保管場所まで自律移動を行います。レーザーによる障害物検知機能が付いているため、高い安全性で作業者との共存が可能です。
ピッキングが終わった商品の運搬も行ってくれるため、移動にかかるタイムロスを削減し、ピッキング作業を効率化できます。
3. ラピュタAMRの導入で改善した事例を2つ紹介
こちらでは、当社が提供する「ラピュタAMR」でピッキング作業を改善した事例を2つ紹介します。どちらも生産性の向上につながっており、自動化に悩む事業者様は、ぜひ参考にしてみてください。
- 日本通運の改善事例
- 京葉物流倉庫の改善事例
3-1 日本通運様のピッキング作業改善事例
日本の物流業界の中でも最大手となる日本通運様に、10台のラピュタAMRを導入しました。ピッキング時に行ったり来たりする必要がないため、業務スピードを向上させることに注力し、省力化を実現しています。
導入後も検証・改善を重ねることで、課題の解決につなげています。物流コストを抑えるうえでも、月額定額制サービスでの導入が効果的でした。
3-2 京葉物流倉庫様のピッキング作業改善事例
関東一円に多くの物流倉庫をもつ京葉流通倉庫の岩槻倉庫様に、20台導入いたしました。従業員の確保が難しい状況であり、現実的な省人化の選択肢としてロボット導入を決断されています。
導入にあたって「50Lのオリコンを載せられるサイズ」が絶対条件でしたが、対応できるサイズにカスタマイズし、導入を実現しました。導入後は生産性の向上を実感いただいていますが、より良い状態を構築するため、日々改善に努めています。
4. まとめ
ピッキングは改善の余地が多い分、すべてを最適化することが難しい作業です。自社の課題を洗い出し、優先順位をつけて、できるところから改善に努めましょう。
その際、この記事で紹介した効率化する方法を実践してみてください。自動化はハードルが高いと思われがちですが、当社が提供するサブスクリプションサービスなら導入コストがかかりません。
プラスオートメーションでは、ピッキング作業の改善方法や、自動化に関するご相談をお受けしています。
|
などのお悩みやお考えがありましたら、下記のフォームよりお気軽にお問い合わせください。