【パターン別】物流業務の改善事例12選!倉庫の改善点を課題とセットでご紹介
「物流業務を改善したい」と考えていても、何から始めたらよいか迷う方は多いのでは?本記事では、物流倉庫で起こりうる課題と改善事例を12個厳選して紹介します。ロボット導入などの物流DXやすぐに実践できる管理面の改善などをまとめたのでぜひ参考にしてみてください。
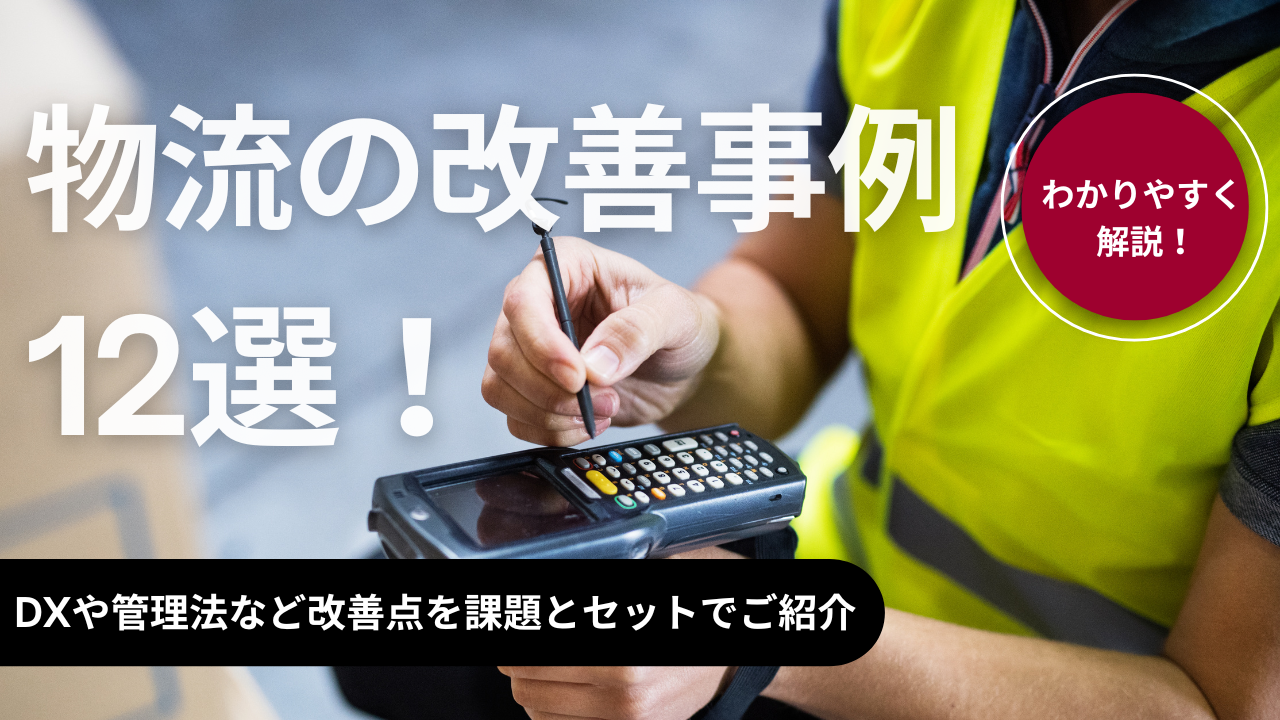
1. 業務効率を改善した事例3選
業務効率を改善した事例を3つ紹介します。
1. 倉庫管理システムの導入で無駄を削減 2. 専任者を配置して従業員による手順のバラつきを解消 3. アウトソーシングでリードタイムを短縮 |
1-1 倉庫管理システムの導入で無駄を削減
【課題】
ある小規模な倉庫では、在庫置き場が煩雑になりがちでした。取り扱う商品が増えるに連れ、熟練者しか在庫のロケーションを把握できない状況になり、商品を探す時間が余計にかかっていた点が課題でした。
【改善点】
倉庫管理システム(WMS)を導入してロケーション管理を徹底することで、新人でもロケーションが分かりやすい仕組みを整えました。倉庫全体のレイアウトを見直して動きやすい導線に組み直し、作業効率の向上にもつなげています。
1-2 専任者を配置して従業員による手順のバラつきを解消
【課題】
ある倉庫では、決められたマニュアルがあっても手順が守られておらず、出荷ミスがなかなか減らないことが課題でした。
【改善点】
パート社員のリーダー・サブリーダーを各部署ごとに決めて、正しいルールを徹底するように管理・指導を行う仕組みを整えました。その結果、自己判断で作業する人が減り、品質が向上。また、分からないことをリーダーにすぐに聞けるようになり、社員を探す手間や必要が少なくなりました。業務効率も大幅に改善しています。
1-3 アウトソーシングでリードタイムを短縮
【課題】
アパレル業界でECサイトを運営するブランドでは、流行に合わせて商品を仕入れても販売リードタイムが長くかかってしまっていました。ささげや縫製加工などの各工程を委託する場所が異なるため、委託先の拠点間の輸送が生じ、それぞれの管理が必要な状態でした。
【改善点】
フルフィルメントタイプの物流センターにアウトソーシングすることですべて解決。ささげ・縫製加工・在庫管理・出荷・お問い合わせ対応など、すべての業務を一元管理できる体制を整え、販売リードタイムを大幅に短縮しています。
2.頻繁に発生するミスを改善した事例3選
頻繁に発生するミスを改善した事例を3つ紹介します。
|
2-1 ハンディターミナルの導入で人為的ミスを軽減
【課題】
目視でチェックを行っている倉庫では、商品の取り違えや数量違いなどの見間違いによるミスがなかなか減らないことが課題でした。
【改善点】
ハンディターミナルを導入することで正確性が上がり、人為的ミスが大幅に軽減。入れ忘れが多かった付属品にもバーコードを付け管理方法を改善しました。
2-2 在庫管理システムの導入で賞味期限管理を見える化
【課題】
ある輸入品を扱う倉庫では賞味期限間近の商品を発送してしまい、百貨店から厳しいクレームを受けてしまいます。海外の商品は賞味期限の表示を読みにくいものも多く、目視での管理に限界を感じていました。
【改善点】
賞味期限管理ができる在庫管理システムを導入し、見える化しました。消費期限・賞味期限が基準値を超えた場合、アラートでお知らせしてくれる仕組みです。出荷時にチェックする手間も省けます。発送先によって異なるルールにも対応できるため、賞味期限管理がしやすくなりました。
2-3 マニュアルの作成で作業手順の標準化を徹底
【課題】
ハンディターミナルを使っているのに出荷ミスが減らない倉庫では、検品のタイミングや操作方法が人によって異なることが悩みでした。そのせいで「人によって教え方が違う」という問題も抱えています。
【改善点】
マニュアルの作成で作業手順をルール化し、作業の標準化につなげました。出荷ミスが減り、生産性も向上しています。マニュアルがあることで新人教育がしやすくなり、教育にかかる時間も短縮できました。
3. 従業員の負担を改善した事例3選
従業員の負担を改善した事例を3つ紹介します。
|
3-1 ローテーションで持ち場によって異なる負担の軽減
【課題】
複数の取引先の商品を取り扱う倉庫では、各作業の担当者がほぼ固定されている状態です。重量のある商品を取り扱う部署、冷暖房から離れた部署など負担の大きい部署から度々不満の声があり、倉庫内の雰囲気が悪くなっていました。
【改善点】
従業員に複数の業務を覚えてもらい、偏らないようにローテーションすることで負担の軽減を図りました。ローテーションにより、繁忙期・閑散期に合わせた人員調整がしやすくなり、管理工数を削減。現場の雰囲気が良くなり、離職率の低下にもつながっています。
3-2 2段台車の導入で腰への負担を軽減
【課題】
棚からパレットへの移動、作業台から台車への移動など、荷物の上げ下げによって腰の痛みを訴える人が多いことが問題になっていました。
【改善点】
2段台車を増やし、上げ下げする動作を少なくしました。その結果、腰への負担が和らぎ、ケガのリスクが減少しています。
3-3 連絡事項を書面で共有して伝達漏れを防止
【課題】
従業員の多い倉庫では、人によって出勤時間や出勤日数が異なるので、変更点や注意点の伝達が漏れてしまうことが悩みでした。
作業者は毎日ローテーションで入れ替わるため、誰に何を伝えたのか分からなくなってしまいます。ホワイトボードに書いても流し読みされてしまい、ひとりひとりにきちんと伝えることに限界を感じていました。
【改善点】
連絡事項を記載した名簿を作成し、作業前に必ず目を通してサインを入れる習慣をつくることで改善しています。サインを見れば誰がどこまでの情報を知っているのか判断しやすいので、伝達漏れを気にせず作業に集中できるようになりました。また、サインを入れることで従業員の意識も高まっています。
4. 当社のロボット導入で物流倉庫を改善した事例3選
当社プラスオートメーションでは、物流向けのロボットサービスを月額定額のサブスクリプションで提供しています。ロボットを導入するだけでなく、導入効果を出すまで並走するサービスです。
ロボットの導入は、人手不足・業務のムダ・作業のミスなど、さまざまな問題の改善につながります。こちらでは、当社のロボット導入で物流業務を改善した事例を3つ紹介しますので、ぜひご確認ください。
4-1 ZOZOBASE習志野1に「t-Sort」280台を省スペースで導入
ファッション業界で知名度の高いZOZOの大型物流拠点の1つであるZOZOBASE習志野1様に、仕分け作業をサポートする「t-Sort」を280台導入いたしました。
時間がかかってミスが起こりやすい仕分け作業を自動化できれば、ミスを削減し、業務効率を大幅に改善することが可能です。今回はロボットの走行ステージを2段式にすることで、省スペースで大規模な導入を実現しています。
人件費を抑え、業務効率や品質を向上させることに成功しました。
4-2 山善に「t-Sort」を導入して省人化を実現
生産財と消費財を扱う専門商社株式会社山善のロジス関東様に、「t-Sort」を24台導入いたしました。
仕分け先の間口を50シュート分用意し、1時間あたり約1,900投入の仕分け作業を行います。人の手だと時間がかかる仕分け作業をt-Sortに任せることで、倉庫の省人化を実現できました。
4-3 日本通運に「ラピュタAMR」を導入して省力化を実現
日本の物流業界の中でも最大手となる日本通運様に、ピッキング時の運搬をサポートする「ラピュタAMR」を10台導入いたしました。
導入後も検証・改善を重ね、省力化を実現しています。ピッキング時に行ったり来たりする必要がないため、業務スピードを上げることに注力できるようになりました。人員確保が難しい物流業界の課題の解決につながっています。
また、顧客満足を獲得するには、生産性を高め、物流コスト自体を下げていかなければなりません。その課題を解決する糸口としても、RaaSによるラピュタAMRの導入が効果的でした。
5. まとめ
今回は、物流業務の改善事例をまとめて紹介しました。管理面の変更やロボットの導入など解決方法は様々です。自社に合った解決方法を試してみましょう。
プラスオートメーションでは、物流業務の改善に関するご相談もお受けしています。次のようなご要望がございましたら、下記の相談フォームよりお気軽にご連絡ください。
|