【効率化】倉庫作業の8つの改善策!荷役・出庫作業の改善法もまとめてご紹介
倉庫内作業を効率化するためには、さまざまな角度から倉庫内の問題点を洗い出し、どのように改善したいのか、明確な目標を定めることが大切です。 本記事では、倉庫を効率化する方法を詳しく解説します。倉庫内で重要な役割を担う「荷役」「出荷作業」を改善する方法も紹介していますので、ぜひ最後までご覧ください。
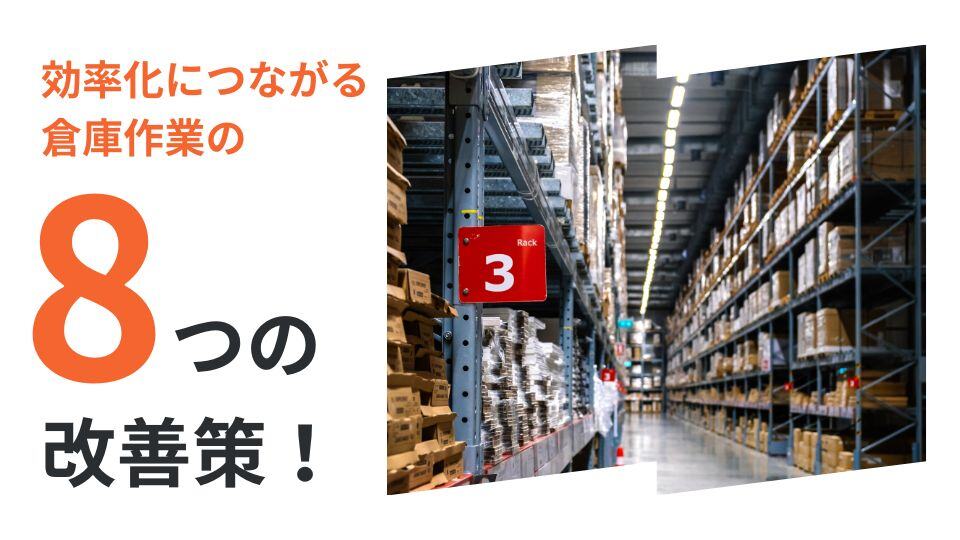
1. 倉庫全体を効率化する8つの改善策
倉庫内作業を効率化するためには、さまざまな角度から業務全体を見直すことが大切です。こちらでは、8つの改善策を紹介します。それぞれ詳しく解説しますので、改善できる部分がないか確認してみましょう。
|
1-1 5Sの導入・徹底
5Sは「整理・整頓・清掃・清潔・しつけ」の総称です。倉庫内をきれいな状態に保つことを従業員に徹底し、倉庫環境の改善につなげます。
5Sによって倉庫内がきちんと整理されていれば、商品を探しやすくなるでしょう。業務効率が上がるだけでなく、商品の取り違えるリスクが減り、誤出荷の軽減にもつながります。
また、多くの人や荷物が行き来し、さまざまなマテハン機器が稼働する倉庫内は、ホコリが発生しやすい場所です。5Sを徹底することで商品を汚れから守り、また、職場環境も改善されるでしょう。
1-2 倉庫レイアウトの見直し
作業効率・保管効率を考えたレイアウトになっているか、無駄な保管コストが発生していないか、倉庫内のレイアウトを見直しましょう。入荷から出荷まで、スムーズに行えるように考慮することが大切です。
また、一時的に商品を保管できる空きスペースを確保しておくことも重要です。繁忙期や閑散期を意識し、どのように対応すべきか考えましょう。レイアウトは一度決定すると途中で変更することが難しいため、商品の流れをきちんと把握したうえで設計する必要があります。
1-3 ロケーションの見直し
ロケーションは、作業者にとって動きやすい導線で、分かりやすい番号を付けることが重要です。出荷頻度の高い商品を取り出しやすい場所に置く、類似商品は離しておくなど、商品に適した管理方法を考えましょう。
その際、人がすれ違えるように余裕をもって通路幅を設定することも大切ですが、すべて広くすればいいわけではありません。歩数が増えるリスクや保管効率も考慮し、ABC分析などを用いて重要度の高い商品を見極めることも大切です。
さらに、棚やピッキングリストを見やすくするための工夫があるほど、より生産性が向上します。必要な情報だけを分かりやすく表示させましょう。
1-4 マテハン機器の見直し
倉庫内で使用しているマテハン機器の見直しも、効率化につながるポイントです。「商品が取り出しにくい」「姿勢がきつくて腰に負担がかかる」など、作業者が使いにくさを感じている可能性があります。
また、倉庫の作業効率と保管効率を考慮して、適切なマテハン機器を用いることが重要です。固定ラックの1段ごとの幅が広くて無駄なスペースがあったり、ハンドリフトが入らないパレットが多かったり、スムーズな業務の妨げになっている部分があるかもしれません。
1-5 各業務のルール化
どの業務においてもルール化は重要です。作業マニュアルを作成し、共有しましょう。
作業マニュアルを作成するときは、現場の声を聞き、作業手順を見直すことも大切です。倉庫全体がルール化されることで、人によってやり方が違うという問題が改善されます。慣れない作業者も手順を再確認できるため、ほかの作業者に聞く手間が省けるでしょう。
また、マニュアルは単に手順を文字で記載するだけでなく、写真などを用いることでより分かりやすくなります。変更点は随時更新し、やりにくい部分がないか定期的に見直すことが、より効率化につながるポイントです。
1-6 人員調整ができる仕組みの構築
複数の業務を請け負っている倉庫では、スムーズに人員調整ができる仕組みを整えておくことが重要です。各部署で業務終了時間にばらつきがある、特定の人しかやり方が分からない仕組みになっているといった状況をなくしましょう。
スムーズに人員調整を行うためには、倉庫全体の進捗状況を把握できる工夫が必要です。各部署の担当者が、定期的に事務所のホワイトボードに終了予定時刻を記入・更新するなど、人員配置を決める担当者が分かりやすいようにしましょう。
また、作業者が複数の業務をローテーションで行える仕組みをつくることも大切です。重い荷物が多い部署、寒暖の差が激しい部署などを考慮して、バランスよくローテーションを組むことで離職率の低下にもつながります。
1-7 トラブル時の原因究明の徹底
万が一誤出荷などのトラブルが発生した際は、原因究明することが重要です。「大きなトラブルにならなかった」などの理由で、現場への周知や対策を怠ってはいけません。
倉庫環境が整っていなかった、作業手順が守られていなかったなど、トラブルが起こる原因はさまざまです。しかしその背景には「忙しくて手順を守らなかった」「分からないことを聞きにくい環境だった」など、心理的な要因が関わっていることもあります。
もしすぐに必要な商品だったが届かなかった場合、担当者が直接謝罪に行くケースも少なくありません。トラブル時はきちんと対策を考え、作業者全員に周知することが大切です。
1-8 倉庫内の自動化ソリューションの検討
業務効率の改善や人手不足の解決策として、倉庫内の自動化ソリューションを検討するのも良いでしょう。自動化ソリューションといってもさまざまな手段があり、主には以下の5つとなります。
- 自動搬送ロボット(AGV)
- 自律走行搬送ロボット(AMR)
- 自動倉庫システム
- ピッキングソリューション(DAS, GAS, DPS)
- パレタイジングロボット
近年では、多くの倉庫で自動化ソリューションの導入が進んでいます。自動化ソリューションと聞くと多額の導入コストがかかると思われがちであり、なかなか踏み出せない事業者様も多いのではないでしょうか。
当社プラスオートメーションでは、初期費用ゼロ、月額定額制でロボットを提供しています。倉庫にロボットを導入することが目的ではなく、導入効果を出すまで並走するサービスです。多くの倉庫で導入効果を実感いただいていますので、お気軽にご相談ください。
2. 荷役を改善する3つの方法
こちらでは、多くの物流現場で実施されている荷役を改善する方法を3つ紹介します。荷役の遅れはほかの業務に影響します。いかに効率よく、安全に進められるかが重要です。
|
2-1 役割分担を明確にする
役割分担を明確にし、スムーズに作業を行える環境を整えましょう。荷役が滞らないように、各担当者や責任者を配置し、協力し合える環境であることが望ましいです。
また、入荷した商品の検品を荷役担当者が行う場合もあれば、出荷担当者や担当社員が行う場合もあります。商品によって出荷までの流れが異なるため、検品漏れや重複を避けるために基本的な役割分担を決めておくと安心です。
2-2 入荷スケジュールを共有する
入荷スケジュールは事務所のホワイトボードやバース管理システムなどで管理し、共有できる状態にしておきましょう。荷役担当者および誘導する事務員等が入荷スケジュールを把握できる状態でないと、スムーズに荷物を受取れません。
天候や交通状況により、予定通りに荷物が入荷しないこともあります。そのような情報も共有することで、入荷が集中してしまったときでも焦らずに適切な対応ができるでしょう。
2-3 荷役の危険性を周知し、安全対策を実施する
荷役は物流倉庫で欠かせない作業ですが、荷役機械の操作ミスや作業者の不注意による事故が多く、「陸上貨物運送事業における労働災害の75.5%が荷役作業時である」と言われています。
事故の原因は、荷役担当者だけが原因で起こるものではありません。他の作業者の急な飛び出しによるものや、積み方の悪さが原因で起こる荷崩れなど、さまざまな要因が考えられます。
そのため、荷役の危険性を周知することは、倉庫全体で取り組んでいくべき問題です。特に荷役作業者には、厚生労働省が発行する「陸上貨物運送事業における荷役作業の安全対策ガイドライン」に沿って安全対策マニュアルを作成し、指導を徹底しましょう。
3. 出荷作業を改善する3つの方法
こちらでは、倉庫内で重要な出荷作業を改善する方法を3つ紹介します。出荷作業は、顧客との信頼関係に直結する重要な作業です。効率よく作業でき、誤出荷が起こりにくい環境を整えましょう。
|
3-1 作業マニュアルを工夫する
出荷作業は、商材や取引先によって異なるルールが多くあります。作業マニュアルを作成する際は、作業者が悩まないように見やすくするための工夫が必要です。
例えば不良品の基準や類似商品の判別方法など、作業者が出荷時に判断に悩む可能性があるものを写真で載せておくと良いでしょう。ハンディターミナルの手順を細かく定めることも大切です。
3-2 伝達漏れが発生しない仕組みを整える
出荷作業に携わる従業員の出勤時間や曜日はさまざまです。特に出荷作業は伝達漏れが起こりやすいため、作業者全員が変更点などをきちんと確認できる仕組みを整えなければなりません。
例えば連絡事項と名簿を記載したバインダーを用意し、作業前にチェックして名前に丸をつけてもらうといった方法も有効です。サインをすることで作業者一人ひとりの意識が高まり、誰が確認していないか判断しやすくなります。
3-3 ピッキングリストを見やすくする
ピッキングリストの見やすさは、生産性の向上に直結します。必要最低限な情報以外は極力表示させないようにしましょう。なお、必要な情報は以下の3つです。
- ロケーション番号
- 商品番号
- 数量
ロケーション番号や数量など、特に重要な部分は文字を大きくしたり色を変えたりする対策も有効です。作業者が見間違えないための工夫をしましょう。
4. まとめ
倉庫内作業を改善するためには、課題となる部分を細かく洗い出すことが重要です。そして、どう改善したいのかを明確にし、それに適した対策をしていきましょう。ぜひこの記事を参考に、自社倉庫に適した改善策を見つけてみてください。
プラスオートメーションでは、以下のようなご相談もお受けしています。
- 何を優先的に改善すべきか分からない
- 具体的にどう改善したらいいのか分からない
- 自動化で倉庫を改善したい
- マニュアルが定まらない
- 適切なロケーションの組み方が分からない
など、漠然としたお悩みでも構いません。お困りごとやご不明な点がございましたら、お気軽に下記のフォームよりお問い合わせください。