2024年問題への対応 中継拠点の設置や、物流倉庫での在庫積み増しによる、輸送負担の軽減
トラックによる輸配送にかかる負担を軽減するために、物流倉庫に求められる役割や機能にも変化が生まれてきています。どういった変化があるのか、そしてその変化を実現していくためにどのような方法があるのかを考察します。
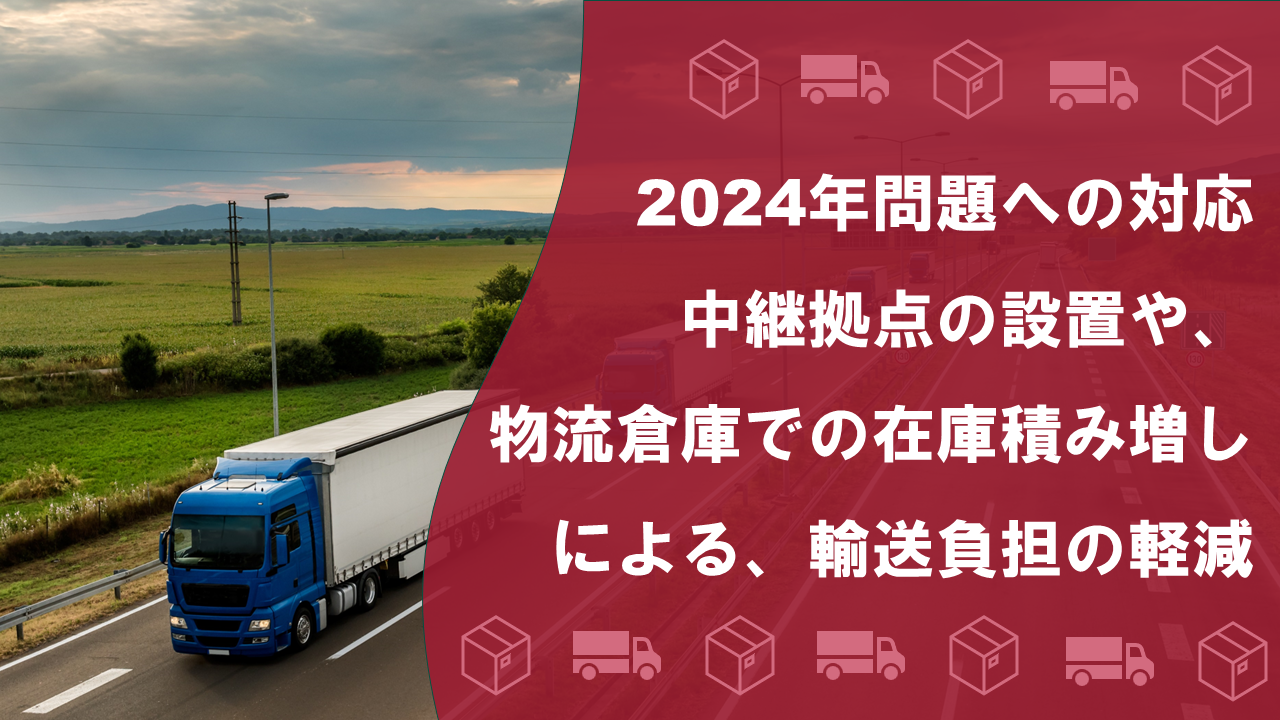
2024年問題※の影響により、それまで行われていた、トラックによる長距離輸送の継続が難しくなると考えられます。以前の記事では、トラックが物流倉庫において、荷物の積み降ろしが完了するまで待機しなければいけない時間をいかに短縮するか、そのためにどのような対応策があるかを考察しました。トラックの待機時間が短くなれば、その分だけ走行時間に充てて輸送可能な距離を延ばすことができるため、これは物流倉庫として実施すべき、2024年問題への重要な対応と言えます。
これに加えて今回は、物流倉庫の拠点配置を見直したり、保管能力を大きくしたりすることによって、荷物の輸配送を担うトラックにかかる負担を軽減する方法について考えてみたいと思います。
※2024年問題とは、2024年4月1日よりトラックドライバーの時間外労働に年間960時間の上限規制が適用されることで、トラックの長距離・長時間の運行ができなくなること、そしてトラックドライバーの人材不足と合わせて、社会全体で荷物の輸送能力が減少してしまうことを指します。
中間拠点の設置による、輸送距離の短縮
長距離ルートを分割して中継輸送へ
2024年問題の影響で、トラックドライバーの残業可能な時間が1日あたりで考えると4時間くらいになるため、運行時間が12時間を超えるような長距離輸送は難しくなってきます。荷物の積み地、降ろし地のそれぞれで待機時間も発生することを考えると、東京・大阪間くらいは運行が可能そうですが(ただし宿泊を伴う)、それよりかなり長くなってくると成立が難しくなることが想定されます。
この状況への対策として、従来は長距離だったルートのどこか途中に中継拠点を置いて、複数の中距離程度のルートに分けてしまう、中継輸送という方法があります。
中継輸送のパターン
(出典:国土交通省)
中継輸送のパターンには、次のようなものがあります。
・中継拠点でドライバーが交代して、車両は同じままで運行する。(ドライバー交代方式) ・コンテナ輸送の場合に、中継拠点でヘッドを交換する。(トレーラー・トラクター方式) ・中継拠点において、車両間で荷物を積み替える。ドライバーとトラックの組み合わせはそのまま。(貨物積み替え方式) |
国土交通省がまとめた「中継輸送の取組事例集」に、それぞれの方式の詳しい内容や実際の事例がたくさん紹介されていますので参考にされてください。国土交通省が、中継輸送の普及を図るため、先行して取り組まれている物流事業者や荷主の事例を募集して、それに応募のあったものをまとめた事例集になります。
中継輸送は、2024年問題に対する真正面からの対応と言える内容で、事例が集まっていることからもわかるように、既にこのような取り組みに着手している物流事業者も多くあります。ある大手物流事業者の方にお話を伺うと、中継輸送に対応することによって次のような負担が生まれるが、それでもやはり取り組まざるを得ない、ということでした。
・中継拠点を配置するコストが掛かる。 ・トラックの台数もドライバーの人数も、従来よりも多く必要になる。 ・中継拠点を経由する運行ルートについて、より数の多いトラックとドライバーを組み合わせて、複雑な配車計画を立てて管理しなければならない。例えばドライバー交代方式の中継輸送を行う場合は、交代前後の予定も上手く計画する必要がある。 |
また一緒に、ドライバー一人当たりの給与は、労働時間が短くなれば(そして単価が同じであれば)、その分はどうしても下がってしまう、というお話もありました。
物流倉庫での在庫積み増しによる、輸送負担の軽減
トラック輸送の頻度を下げて負担を軽減
トラックによる輸送の頻度を下げて、トラックにかかる負担をそもそもから軽減する、という対策もあります。
例えば毎日トラックが運行していたとしたら、単純にそれを2日に1回などより低い頻度に減らす、という方法です。輸送の頻度が下がる代わりに、1回あたりの入出荷の量を増やすことになって、トラックによる輸送の積載効率が上がる、という効果も見込まれます。
トラックの貨物積載率が平均で40%以下になっていることも課題であるため、この改善にもつながると期待されます。トラックによる輸送の負担を軽減しながら積載効率も上がるというのは、共同配送(複数の荷主の荷物を同じトラックで配送する)と同様の効果と言えます。
トラックにかかる負担が軽減する一方で、物流倉庫にとっては、在庫が増減する幅が大きくなり、在庫を保管する期間(在庫の滞留期間)も長くなるため、おそらくは従来よりも多くの在庫を保管しておく必要が出てくる、いわゆる在庫の積み増しも必要になってくると考えられます。
<トラック便数の抑制と在庫の流れの関係>
(出典:船井総研ロジ株式会社「2024年問題における荷主企業の在庫コントロール強化の重要性」)
在庫を積み増すためにはより広い保管スペースが必要になりますが、できるだけ元と同じ倉庫の保管効率を向上することで対応したいところです。ここから、倉庫の保管効率を上げる方法について紹介します。
保管効率を上げるための、一般的な方法
保管スペース(面)を広げる
(出典:ダイフク「移動ラック 重量級移動棚」)
荷物の保管のために使えるスペースを大きく確保できるよう、その他のスペース、例えば梱包等の作業を行うスペースや、通路を最小限に設計する、という方法です。保管機器として移動ラックを使えば、複数のラック列に対して通路は1列分だけで済むため、保管スペースをより大きくできます。
高さを活かす
天井高が5メートルくらいある倉庫であれば、高さを活かして保管効率を上げることも有効です。パレット保管の荷物であればパレットラックやネステナーを使えば3段、4段と積み重ねることができます。ケースやバラ品を保管するラックも、一般的なものは高さが2メートル前後ですが、3メートル以上ある高層ラックを用いることもできます。
なお、高さを活かすことで保管効率はアップしますが、高い所の荷物の出し入れには、フォークリフトやピッカーリフト、昇降ステップといった機器が必要になる分、低い所での作業と比較して手間が掛かりますし、作業できる人員が限られることもあり、保管効率とのトレードオフになることには注意が必要です。
物流ロボットも、保管効率を重視するタイプが増加
10年ほど前に、初期のGTP方式ロボットが登場
2010年代前半に、人が保管エリアまで荷物を取りに行くのではなく、荷物の方が人のいる作業スペースまで移動してくる、いわゆるGTP(Goods to Person)方式の物流ロボットが登場して、人の歩行にかかる労力と時間を削減する革新的なソリューションとして注目を集めました。当初のGTP方式のロボットは、2メートルくらいの高さのラックを持ち上げて、ラックごと荷物を作業スペースまで運ぶというものでした。
<初期のGTP方式ロボット>
(出典:Boston Globe「kiva」)
写真で見るとわかるように、広い面積を使いながら、ラックの高さが2メートルくらいしかないため、その上部の大きな空間が活用されません。特に、土地が限られてスペースが希少な日本では、このことは当初から課題と考えられていました。
保管効率を重視するタイプのロボットが増加
初期のGTP方式ロボットが登場してから10年ほどが経過する中で、より保管効率を重視するタイプが増加してきました。形状や荷物の取り扱い方法には色々な方式があるのですが、大きく共通する特徴として、高さを活かしながら、ラックよりも小さいコンテナ(トート、ケースなどとも呼ばれます)の単位で緻密に荷物を取り扱うことができる、ということがあります。
代表的なものをいくつか紹介したいと思います。
・Autostore
(出典:株式会社オカムラ「オートストア」)
コンテナを高密度に、高さも使って集積保管。ロボットがコンテナを搬送します。
・PopPick
(出典:株式会社ギークプラス「PopPick」)
高層のラックにコンテナを積んで、ラックごと搬送します。
・HAI PICKシリーズ
(出典:hai robotics「HAI PICKシリーズ」)
高層ラックに保管されたコンテナを、ロボットが取得して搬送します。
平面型仕分けロボット「t-Sort 」と好相性
ここまでに紹介した、入出荷と保管を担う物流ロボットで、出荷時のピッキングを行った後は、一般的には仕分けの工程が続きます。これらのロボットと、当社プラスオートメーションが提供する、小型仕分けロボットを用いた次世代型ロボットソーター「t-Sort」は非常に相性がよく、連携して導入される事例も多くあります。 t-Sortはレイアウトの自由度が高く、仕分け先の間口数を、GAS(Gate Assort System)より多く※設計しても上手く運用できます。
ラックごと搬送するタイプのロボットがピッキング作業場に来た時に、そのラックに保管されたアイテムがヒットする(=ピッキングの対象になる)確率が、仕分けの間口数が多い分、高くなります。ロボットの運用効率が高くなると言えます。
※GASでは間口数は30までくらいが適正であり、それ以上多いと作業者が歩行を伴いながらゲートに荷物を投入する際の作業負担が大きくなり、作業効率が下がると考えられます。これに対してt-Sortでは、仕分け作業が自動化されるため、間口数が多くても作業者の負担は増えません。
立体型仕分けロボット「t-Sort3D 」で更にスペース効率をアップ
間口数を多くすればそのためのスペースも広くなってしまうのですが、立体型仕分けロボット「t-Sort3D」であれば高さを活かしてスペース効率を上げられるため、この心配もありません。 2023年1月にリリース しました、当社プラスオートメーションと株式会社ギークプラスの協業は、このような相性のよさ、シナジーを目指したものです。
まとめ
2024年問題に対して、物流倉庫として実施できる対策として、中継拠点を設けて長距離輸送を分割すること、在庫の積み増しをして入出荷の頻度(トラックの運行頻度)を下げること、を紹介しました。
負担が増してしまう部分は確かにありますし、問題への対策、というとネガティブな印象が先行してしまいがちですが、本文でも触れましたように、トラックの貨物積載率や物流倉庫の保管効率の改善につながるような、ポジティブな側面もきっと見出すことができます。2024年問題を前に、荷主と物流事業者とで利害関係を一致させて、協調した改善検討もしやすい環境になると思われますので、ピンチはチャンスの精神でぜひ前向きな姿勢で取り組んでいきましょう。